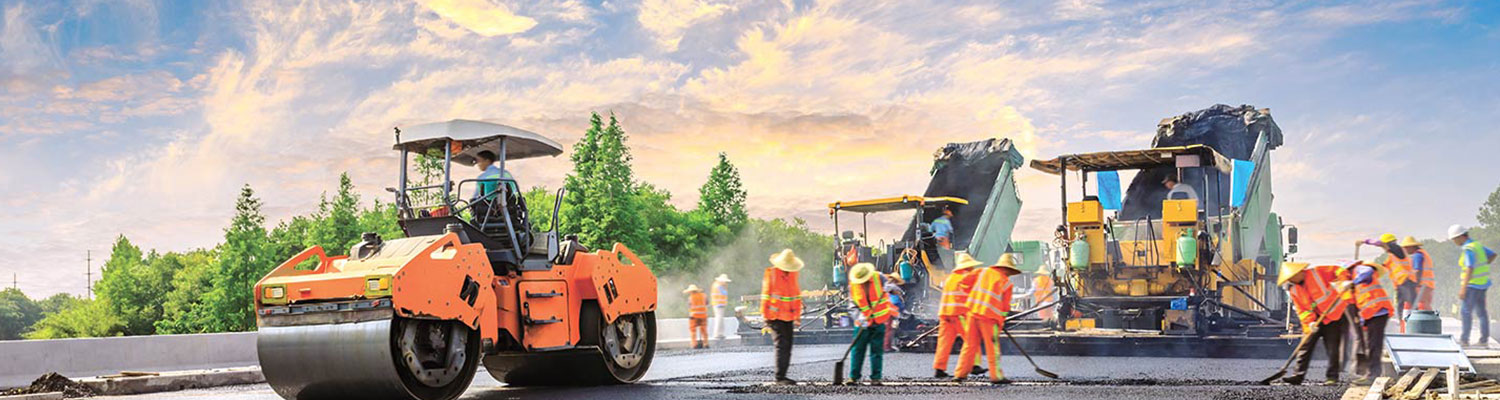
Asphalt Drum Mix Plant Manufacturer
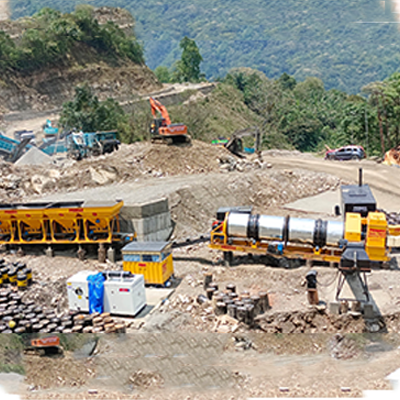
High-Quality Asphalt Drum Mix Plants for Superior Road Construction
An Asphalt Drum Mix Plant is an essential machine in road construction, ensuring the continuous and efficient production of hot mix asphalt. This equipment plays a critical role in highway construction, urban road development, airport runways, and infrastructure projects.
As a trusted Asphalt Drum Mix Plant Manufacturer, Primax Equipment provides high-performance, fuel-efficient, and durable drum mix plants to contractors and road construction firms across West Bengal, Kolkata, Bihar, Odisha, Jharkhand, and all over India.
Why Choose Primax Equipment’s Asphalt Drum Mix Plants?
At Primax Equipment, we specialize in advanced asphalt mixing technology to help you achieve seamless and long-lasting road construction.
✅ Advanced Drum Mixing System – Ensures consistent quality and uniform asphalt mix.
✅ Heavy-Duty Construction – Designed for high durability and long service life.
✅ Fuel-Efficient Burner System – Reduces operational costs with low fuel consumption.
✅ Precise Aggregate & Bitumen Weighing – Provides accurate mix proportions.
✅ Customizable Configurations – Available in various capacities for different project needs.
✅ Easy Operation & Low Maintenance – Ensures hassle-free performance.
Types of Asphalt Drum Mix Plants We Manufacture
1. Mobile Asphalt Drum Mix Plant
Ideal for temporary and remote road construction projects, ensuring quick and efficient asphalt production.
Key Features:
✔️ Compact and portable design for easy transportation.
✔️ Integrated control system for user-friendly operation.
✔️ Quick installation and dismantling for faster project execution.
2. Stationary Asphalt Drum Mix Plant
Perfect for large-scale and long-term road construction projects with high production capacity.
Key Features:
✔️ Heavy-duty components for extended service life.
✔️ High-capacity output for continuous asphalt production.
✔️ Advanced pollution control system for eco-friendly operations.
3. Automatic Asphalt Drum Mix Plant
Designed for fully automated and precision-based asphalt production, ensuring maximum efficiency and high-quality mix.
Key Features:
✔️ PLC-based control panel for accurate mix design.
✔️ Automatic temperature control system for consistent output.
✔️ Integrated conveyor system for smooth material flow.
Applications of Asphalt Drum Mix Plants
Our Asphalt Drum Mix Plants are widely used for:
✔️ Highway & Expressway Construction – Delivers durable and smooth asphalt surfaces.
✔️ City & Rural Road Development – Ensures long-lasting roads with high bonding strength.
✔️ Airport Runways & Taxiways – Provides uniform asphalt mix for heavy traffic loads.
✔️ Industrial & Commercial Road Projects – Ideal for strong and reliable pavements.
Why Contractors Trust Primax Equipment?
As a leading Asphalt Drum Mix Plant Manufacturer, we focus on delivering robust, cost-effective, and energy-efficient drum mix plants tailored for Indian road construction requirements.
🔹 Years of Experience – Trusted by leading infrastructure developers.
🔹 Superior Engineering & Technology – Ensures high efficiency and durability.
🔹 Competitive Pricing – Affordable asphalt drum mix plants with premium quality.
🔹 Nationwide Delivery & Installation Support – Serving West Bengal, Kolkata, Bihar, Odisha, Jharkhand & all over India.
🔹 Reliable After-Sales Service & Spare Parts Support – Providing seamless maintenance solutions.
Serving West Bengal, Bihar, Odisha, Jharkhand & All Over India
We cater to road construction companies, government infrastructure projects, and private contractors across West Bengal, Kolkata, Bihar, Odisha, Jharkhand, and other regions in India. Our strong delivery network and expert technical team ensure hassle-free installation and operational support.
Get the Best Asphalt Drum Mix Plant for Your Road Construction Needs!
Looking for a fuel-efficient, high-performance, and durable Asphalt Drum Mix Plant? Primax Equipment is your reliable partner for superior road construction solutions.
📞 Call Now: +91 9748421428
📩 Email Us: info@primaxgroup.com